Time-Based Maintenance for Power Transformers
- Augusto Moser
- 4 days ago
- 6 min read
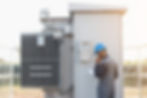
In the field of asset management, particularly for critical equipment like power transformers, maintenance strategies are essential to ensure reliability, safety, and cost-effectiveness. Among these strategies, Time-Based Maintenance (TBM) is one of the most traditional and widely used approaches. This article explores TBM in detail, explaining its purpose, how it works, and its advantages and limitations. Additionally, it provides insights into Corrective Maintenance, distinguishing between minor and major work, and discusses how TBM can help reduce the need for such reactive measures.
What is Time-Based Maintenance (TBM)?
Time-Based Maintenance (TBM) is a preventive maintenance strategy where maintenance activities are performed at predetermined intervals, regardless of the actual condition of the equipment. These intervals are typically based on time (e.g., every six months) or usage (e.g., after a certain number of operating hours). The primary goal of TBM is to prevent equipment failures by servicing or replacing components before they are likely to fail, based on historical data, manufacturer recommendations, or industry standards.
TBM is often contrasted with more advanced strategies like Condition-Based Maintenance (CBM), which relies on real-time condition monitoring to determine when maintenance is needed, and Reliability-Centered Maintenance (RCM), which focuses on identifying and addressing specific failure modes. While CBM and RCM can be more efficient in certain contexts, TBM remains popular due to its simplicity and ease of implementation.
How Does TBM Work?
Determining Maintenance Intervals
The success of TBM hinges on setting appropriate maintenance intervals. These intervals are typically determined using:
Manufacturer recommendations: Equipment suppliers often provide guidelines on when to perform maintenance based on their design and testing.
Historical data: Organizations may analyze past failure data to identify patterns and set intervals accordingly.
Industry standards: Sectors like power generation or aviation often have standardized maintenance schedules based on collective experience.
For instance, a transformer manufacturer might suggest replacing specific components every 10 years or after 100,000 hours of operation. Alternatively, the industry well established yearly maintenance schedule.
General Types of Maintenance Activities
TBM encompasses a range of activities, including:
Inspections: Regular checks to identify wear, damage, or other signs of deterioration.
Lubrication: Ensuring moving parts are properly lubricated to reduce friction and wear.
Cleaning: Removing dirt, debris, or contaminants that could affect performance.
Adjustments: Fine-tuning equipment settings to maintain optimal operation.
Replacements: Swapping out components that are likely to fail soon, even if they are still functioning.
These activities combined with electrical tests, Dissolved Gas Analysis (DGA) and Oil Quality Analysis (OQA) are scheduled at fixed intervals, aiming to catch potential issues before they lead to failures.
Role of Electrical Tests, DGA, and OQA in TBM
Electrical Tests
Purpose: Electrical tests, such as insulation resistance, power factor (or dissipation factor), winding resistance, and turns ratio tests, assess the dielectric and electrical integrity of the transformer’s insulation system and windings. These tests help identify issues like insulation degradation, winding faults, or poor connections.
Role in TBM: In a TBM strategy, electrical tests are typically performed at regular intervals (e.g., annually or every few years) based on manufacturer recommendations, industry standards (e.g., IEC or IEEE), or operational history. These tests are preventive, aiming to detect potential issues before they lead to failures.
Example: A power factor test might be scheduled every two years to check for insulation moisture or contamination, even if no issues are suspected.
Dissolved Gas Analysis (DGA)
Purpose: DGA involves analyzing gases dissolved in the transformer’s insulating oil to detect incipient faults, such as overheating, partial discharges, or arcing. It is a key diagnostic tool guided by standards like IEC 60599 and IEEE C57.104.
Role in TBM: DGA is often incorporated into TBM schedules, with oil samples taken at fixed intervals (e.g., annually or semi-annually) to monitor gas levels and trends. Regular DGA helps identify early signs of faults, allowing for timely interventions before major failures occur.
Example: A utility might schedule DGA every 12 months for critical transformers, using tools like the Duval Triangle to interpret results and assess fault severity.
Oil Quality Analysis (OQA)
Purpose: OQA evaluates the physical and chemical properties of transformer oil, such as moisture content, acidity, dielectric strength, and interfacial tension. These properties indicate the oil’s condition and its ability to insulate and cool the transformer effectively.
Role in TBM: OQA is a standard TBM activity, typically performed at predetermined intervals (e.g., every 1–3 years) to ensure the oil remains within acceptable limits. Degraded oil can accelerate insulation wear, so regular testing helps maintain transformer health.
Example: Testing for moisture content might be scheduled annually to prevent dielectric breakdown due to excessive water in the oil.
Our Solutions
HV Assets has a complete solution for monitoring transformers using an advanced water, hydrogen, temperature and pressure sensor, the Basic Care Sensor, and the Early Warning Sensor, measuring hydrogen and temperature. Click here to check the technical data.
Benefits and Drawbacks of TBM
Benefits
Predictability: Maintenance can be planned well in advance, allowing for better scheduling of resources, personnel, and downtime.
Simplicity: TBM is straightforward to implement and manage, requiring less sophisticated monitoring equipment or data analysis compared to CBM or RCM.
Preventive Focus: By addressing potential issues before they cause failures, TBM can reduce the frequency of unexpected breakdowns.
Drawbacks
Potential for Over-Maintenance: Since TBM does not account for the actual condition of the equipment, it may lead to unnecessary maintenance, increasing costs and potentially introducing new risks (e.g., human error during maintenance).
Inflexibility: Fixed intervals may not adapt to varying operational conditions, meaning some equipment might be under-maintained if it degrades faster than expected, or over-maintained if it remains in good condition.
Limited Insight: TBM does not provide real-time feedback on equipment health, which can be a disadvantage for critical assets where early detection of issues is crucial.
Corrective Maintenance: Minor and Major Work
While TBM aims to prevent failures, it cannot eliminate them entirely. Unforeseen issues, such as manufacturing defects, extreme environmental conditions, or operational errors, can still lead to equipment breakdowns. This is where Corrective Maintenance comes into play.
Corrective Maintenance is a reactive approach performed after a failure has occurred. It can be categorized into two types:
Minor Work: This involves small-scale repairs or adjustments that can be completed quickly with minimal downtime. Examples include tightening loose connections, replacing a faulty sensor, or patching a small leak.
Major Work: This refers to extensive repairs, overhauls, or even complete replacements of equipment. Major work is typically required when a failure is severe, such as a catastrophic winding failure in a transformer, necessitating significant downtime and resources.
Role of Corrective Maintenance
Corrective Maintenance is an essential part of any maintenance strategy, as it addresses failures that could not be prevented. However, relying too heavily on corrective actions can lead to increased downtime, higher repair costs, and potential safety risks. Therefore, the goal of preventive strategies like TBM is to minimize the need for Corrective Maintenance, especially major work.
How TBM Reduces the Need for Corrective Maintenance
By performing regular maintenance at set intervals, TBM helps to:
Identify and address wear and tear before it leads to failure.
Replace aging components that are more likely to fail.
Maintain optimal operating conditions, reducing the stress on equipment.
When implemented effectively, TBM can significantly decrease the frequency and severity of failures, thereby reducing the reliance on Corrective Maintenance. However, it is important to recognize that TBM is not foolproof. Failures can still occur due to factors outside the scope of regular maintenance, such as design flaws or extreme events. In such cases, having a robust Corrective Maintenance plan is crucial to quickly restore equipment to service and minimize operational disruptions.
Integrating TBM in a Balanced Strategy
While TBM is effective in many scenarios, it is not a one-size-fits-all solution. For critical assets like power transformers, a balanced maintenance approach that integrates TBM with other strategies, such as Condition-Based Maintenance (CBM) or Reliability-Centered Maintenance (RCM), can offer the best results.
TBM provides a solid foundation of regular, preventive care.
CBM adds real-time monitoring to detect issues early, allowing for more targeted interventions.
RCM ensures that maintenance efforts are focused on the most critical failure modes.
By combining these approaches, organizations can optimize equipment reliability while managing costs effectively. Additionally, having a well-defined Corrective Maintenance process ensures that when failures do occur, they can be addressed swiftly and efficiently.
Conclusion
Time-Based Maintenance (TBM) is a valuable preventive strategy that helps reduce equipment failures through regular, scheduled maintenance activities. Its predictability and simplicity make it a popular choice, particularly for organizations with large fleets of similar assets. However, TBM has limitations, such as the potential for over-maintenance and its inability to adapt to real-time equipment conditions.
Corrective Maintenance, encompassing both minor and major work, remains a necessary component of any maintenance program to handle unexpected failures. While TBM can reduce the frequency of such failures, it cannot eliminate them entirely. Therefore, a comprehensive maintenance strategy should integrate TBM with other approaches, ensuring that equipment is maintained proactively while being prepared to respond effectively when corrective actions are needed.
By understanding the strengths and limitations of TBM and Corrective Maintenance, asset managers can develop a balanced, efficient maintenance program that maximizes reliability and minimizes costs.
Our Solutions
The HV Assets Care Platform is a complete solution for data analysis and diagnostics. It includes all the recommended methods from the IEEE standard, including the Duval Triangle and the advanced Combined Duval Pentagon, integrated in an Asset Management dashboard. It provides a Health Index with individual scores to create an asset ranking. For more information, click here.
References
CIGRE, "Guide for transformer maintenance" (445), 2011.